FAQs
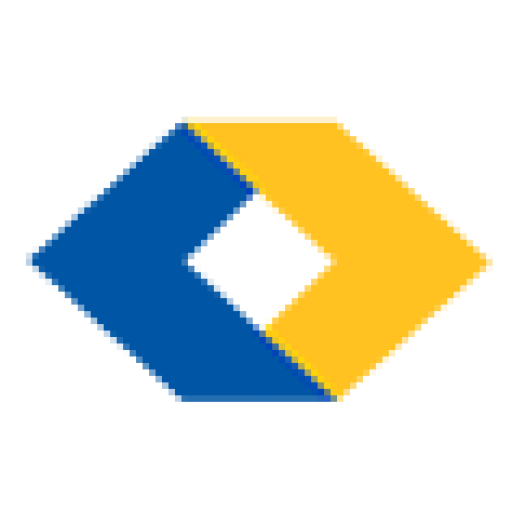
Stock cases, in black, can be ordered in any quantity from 1 to 500. Orders of stock cases larger than 500 pieces are generally run to order and will require a little additional time. Orders for stock cases in colors other than black would need to meet the minimum order quantities and would require production lead time.
Stock cases, in black, can be ordered in any quantity from 1 to 500. Orders of stock cases larger than 500 pieces are generally run to order and will require a little additional time. Orders for stock cases in colors other than black would need to meet the minimum order quantities and would require production lead time.
Stock cases in black are inventoried in our Massillon, Ohio warehouse for shipment within 48 hours of order confirmation. Production lead time for large quantities or cases in colors other than black is typically 2-4 weeks from order confirmation.
We have minimum order quantities for color stock cases. In general cases 13 1/2″ wide and under would require a minimum order of 500 pieces. Cases 15″ to 19″ wide would require minimum orders of 350 pieces and cases with a width dimension wider than 20″ have a 250 piece minimum. These quantities are guidelines only. Please contact Customer Service for minimum quantities on the specific case you need.
There is usually a minimum of 25 pieces for a custom foam order. For additional information, please contact Customer Service or your Territory Sales Manager.
For more information about custom mold orders please contact Customer Service or your Territory Sales Manager.
No problem. Call or email us now. We’ll figure out what you need and how to get it to your right away. In a real pinch, and if our UPS driver hasn’t left yet, we may be able to ship the same day.
PFC cases are made of HDPE (High Density Polyethylene). HDPE provides a good mix of abrasion resistance, impact toughness, resistance to chemicals and strength for a general purpose carrying case. Latches are made of a proprietary blend of Polyolefins specially formulated to give high flexibility and fatigue resistance over an extended temperature range.
HDPE has a working temperature range of -30°F to 150°F. PFC latches are tested over this same temperature range for stretch and fatigue resistance and their ability to withstand shock.
PFC cases are water resistant but not waterproof. All PFC cases are designed with a closefitting interlock which provides a water and dust trap but does not seal the case interior. AllConditions™ cases are weather-resistant and feature our proprietary gasket sealing system to keep your gear clean and dry. In fact, AllConditions™ cases have recently been certified IP53 by a nationally accredited independent testing laboratory.
We stock 2# Charcoal Ether foam and 1.7# Dark Grey Laminated Polyethylene foam in a variety of thicknesses. We can also supply Ether, Urethane or Poly foams in different colors. Check out our foam options for more information.
Although uncolored HDPE is a translucent material when formed, our manufacturing process makes it opaque. All PFC cases have a surface texture to improve scratch resistance. The surface texture also makes it impossible to see through the case.
All PFC cases incorporate our patented mechanical pin and socket hinge. Originally developed in 1972, our hinge has undergone constant improvement and has been licensed to over 30 other companies around the world. Both the pins and sockets are formed during the molding operation to ensure maximum strength and longevity.
We have an on-site recycling operation that allows us to grind plastic and incorporate it back into the manufacturing process. Our black cases can be made using 100% recycled plastic, depending on availability. Regrinding does not affect the quality or durability of the cases.
Developed in the late 1930s, blow molding is a manufacturing process that is used to form hollow plastic parts. It is most commonly used to make plastic bottles. In principal, the basic blow molding process is similar to glassblowing. Plastic resin (pelletized raw plastic material) is melted and formed into a hollow tube or parison which is then placed into a mold. The parison is then inflated using compressed air to form a finished part. In the early 1960s, PFC founder Peter T. Schurman realized that he could combine two hollow blow molded parts to form the lid and base of a portable container or enclosure, and the “double‐wall blow molded carrying case” was born.
All of our manufacturing takes place in the USA. We have two fully-operational plants, one in Ohio and one in Connecticut. Our design and mold engineering is done at our Connecticut headquarters and we source our materials domestically, we don’t subcontract work to other companies, and we don’t outsource anything to foreign manufacturers.
All cases shown on the stock case list are inventoried in black, however, in order to meet your specific marketing needs PFC can manufacture a case in just about any color.