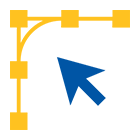
PFC’s design team is your best choice
Given that we developed many of the processes used in the industry today, we understand the requirements for hard cases, aesthetics, and the double-wall molding process better than anybody. We also offer many design features that are not possible with other molding techniques. Our design team creates efficient, effective designs that don’t just look good on a diagram – they translate to great cases: cases that work well and are built to last. The result is more than a design solution: it’s a case that complements, in fact becomes a part of, your product.