It started with a simple kitchen stool
In 1963, Peter Schurman was working on a project to replace the steel and rubber steps on a Hamilton Cosco kitchen stool with a one piece blow molded design. The top of the new step was flat and textured, while the bottom surface was shaped to fit the stool’s metal frame. While holding two prototypes one afternoon, it dawned on Schurman that joining two of those steps together with some sort of hinge would create a rectangular box with interior compartments that could be used as a package – and the double-wall blow molded case was born.
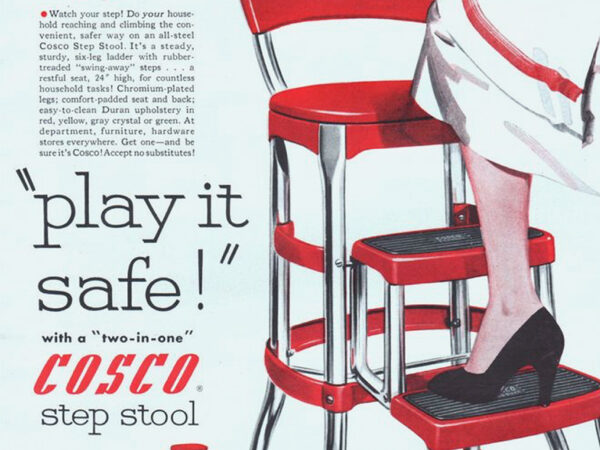
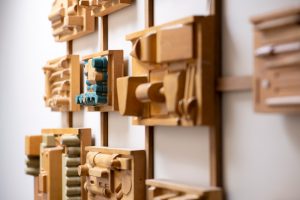
In the following years, Schurman developed his invention further and, in 1966, The Plastic Forming Company (PFC) opened its doors in Woodbridge, Connecticut. Because of their unique combination of extreme durability, product protection, styling freedom, and moderate cost, custom designed double-wall blow molded cases quickly became the preferred method to package a wide variety of consumer and industrial products including hand and power tools, chain saws, camping lanterns, and construction toy sets. The company grew quickly and, to accommodate rapidly growing demand, PFC licensed other companies in the U.S. and in Europe.
Standard Tooling
In the early 1980’s, PFC decided to develop a proprietary line of standard cases and focus on packaging the broad array of products sold by small and medium-sized manufacturers and distributors. PFC cases have now been used to package and protect more than 5,000 different products including professional hand and power tools, portable test instruments and meters, microscopes, surveying transits and other optical devices, heart monitors and medical instruments, educational kits, and more.
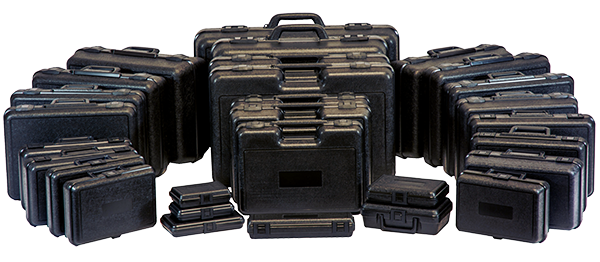
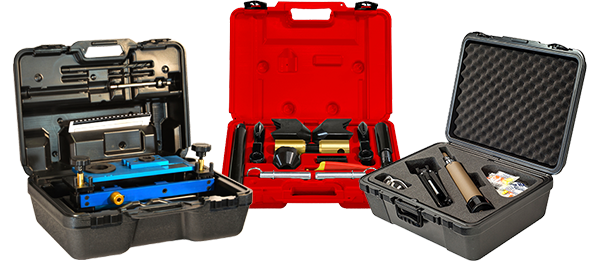
What Makes Us Different
At PFC, we think the answer is to concentrate on the fundamentals – doing everything we can to help our customers meet those challenges when they arise. We’ve focused our entire business – every person, every process, every piece of equipment – to be more responsive and agile. For example, because it is often more difficult for our customers to predict the demand for their products and to know how many cases they will need, where they will need them, and when, we provide just-in-time delivery and logistical assistance. When another customer needed to package a half dozen kits with the same basic tool but with different sets of accessories, we were able to invent and patent a molded “shoe” insert that allowed them to use the same basic case and warehouse a single SKU.
Employee Owned
Since 1989, a significant portion of PFC has been owned by its employees through an Employee Stock Ownership Plan (ESOP).
An ESOP is not simply an employee benefit, it is real ownership, and it gives every PFC employee a stake in how well the company does. Extensive research shows that employees at ESOP companies are more dedicated and work harder; they feel better about themselves, their coworkers and their jobs; and they do a better job serving their customers. That is certainly true at PFC.
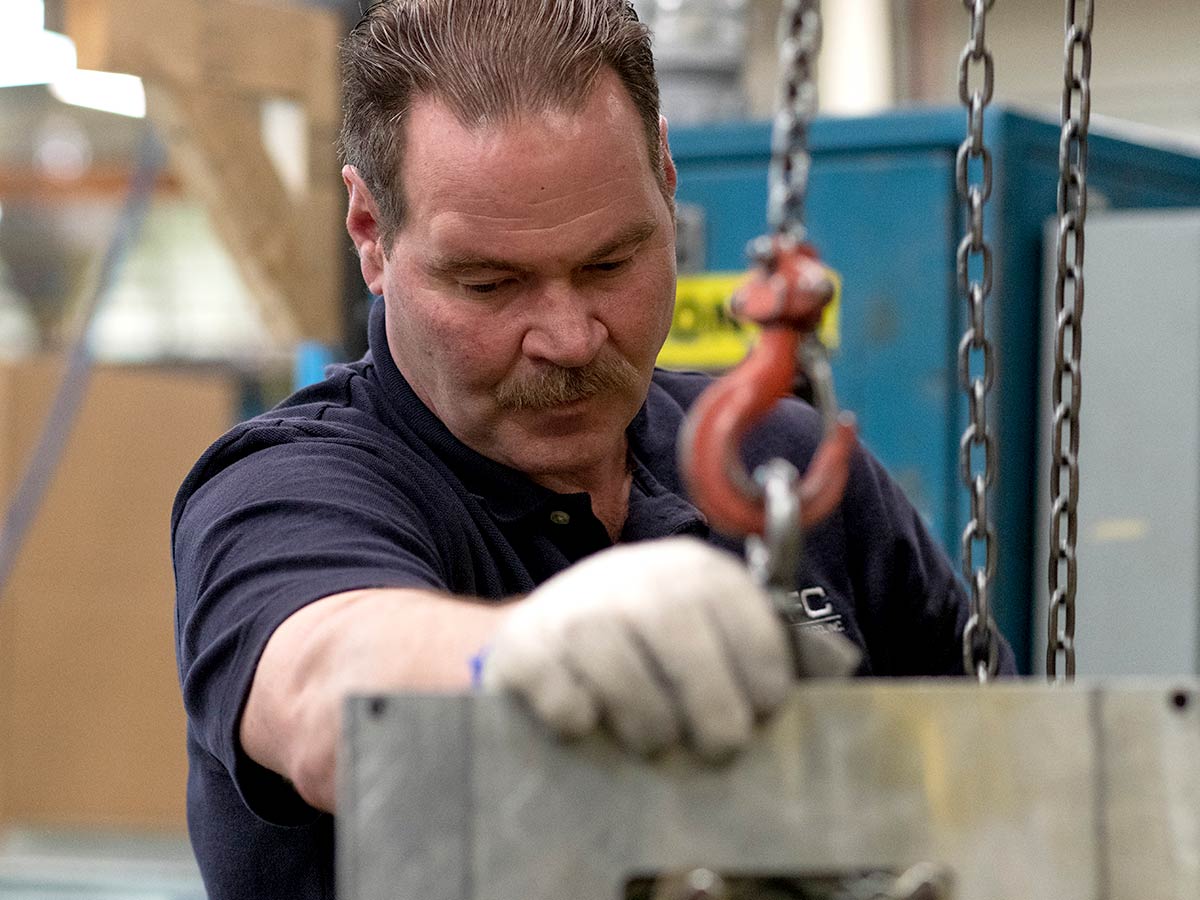
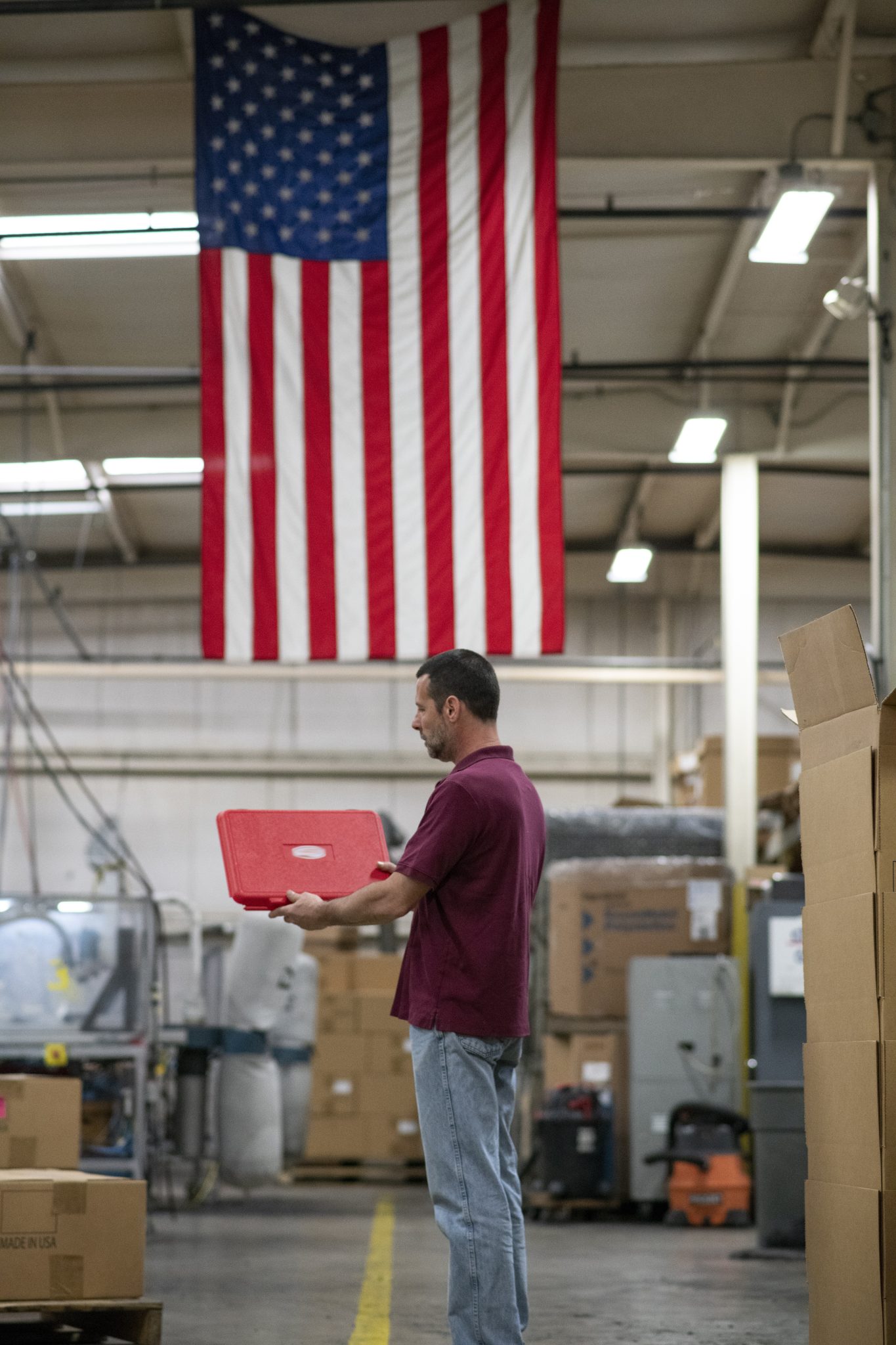
Made in U.S.A.
This year we are celebrating 58 years making cases, and we do everything right here in the U.S.A. – design, mold engineering, and manufacturing. PFC is Headquartered in a 28,800 square foot office and manufacturing facility in Woodbridge, CT. PFC has an additional 40,000 square feet of manufacturing space in Massillon, Ohio.
We source our materials domestically, we don’t subcontract work to other companies, and we don’t outsource anything to foreign manufacturers. The Plastic Forming Company is a proud member of the Made in America Movement.